ข้อมูลสินค้า
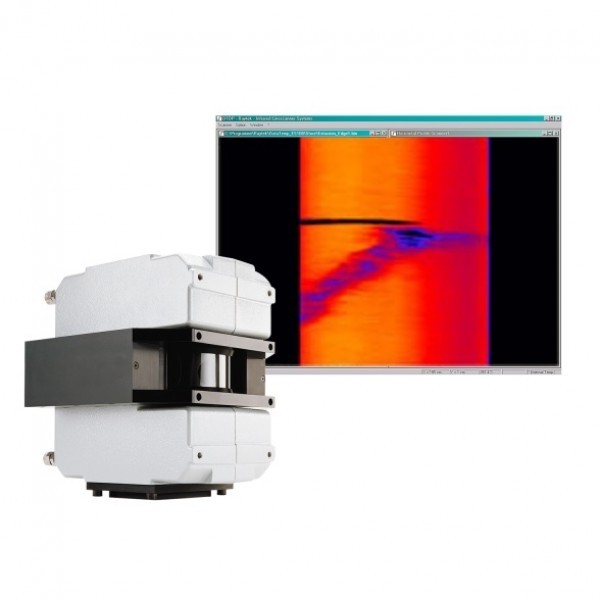
Raytek RAYTES150 Series Imaging System for Continuous Web Processes
Fluke Process RAYTES150 Offers
The ES150 system continuously monitors the web process allowing temperature data to be visualized as a line graph (profile) and a thermographic image. Profiles and images may be printed or archived for analysis.
Through the use of OPC (OLE for Process Control), the ES150 system acts as an OPC server and communicates with many common process control systems. This feature allows the ES150 to move beyond being just a measurement tool and becomes an integral part of the total process control system.
Features
- Reduce Process setup time and automatic quality monitoring
- Early detect die bolt heater problems or plugged role
- Define product-specific configurations and data files
- View complete sheet temperature profile for more effective chill roll control
- Customize and display zones overlayed on thermal image
- Automatically analyze zone temperatures
ES150 Process Imaging Software
The system provides the capability to define any number of sectors corresponding to specific areas across the sheet. Sectors are defined by name, location, and the desired processing of temperature data within the sector (e.g., average, minimum, or maximum temperature).
Applications
In plastic sheet extrusion production, polymers are melted through a slot or flat die (extruded) to form a thin, molten sheet. This sheet is is attracted towards the surface of a chilled roller where it immediately solidifies. The sheet then passes through a series of rollers which will determine thickness and texture before being edge trimmed and cut to the required size (heavy gauge sheet) or wound onto a roller (thin gauge sheet). Extruded plastic sheets are often used for thermoforming into a final shape (for example in the manufacture of refrigerator or freezer internal panels or plastic beverage cups).
In cast film production, polymers are melted through a slot or flat die (extruded) to form a thin molten film. This film is attracted towards the surface of a chilled roller using the force of an air knife or vacuum box, where it immediately solidifies. The film then passes through a series of chill rollers before being edge-trimmed and typically wound on a roll. Some machines will extrude a number of films for a laminated final product.
Continuous process laminating and embossing machines typically heat and cure a number of substrates together before embossing a textured finish to one or both sides. Depending on the finish desired, calendar rolls may also be used to modify smoothness, surface luster and thickness uniformity. Heat energy is added to the process through the use of heated rollers and electric or gas infrared panel heaters.
Specifications
Model |
ES1501MR0 |
ES1502MR0 |
ES150G5R0 |
ES150LTR0 |
ES150MTR0 |
TES150P30R0 |
Range |
600 to 1200°C |
400 to 950°C |
100 to 950°C |
20 to 350°C |
100 to 800°C |
30 to 250°C |
Accuracy |
±0.5% of measured value or ±3ºC (6ºF) whichever is greater |
±2°C (±4°F) |
±3°C (±6°F) |
±3°C (±6°F) |
||
Repeatability |
±2°C (±4°F) |
±2°C (±4°F) |
±1°C (±2°F) |
±1°C (±2°F) |
±2°C (±4°F) |
±1°C (±2°F) |
Spectral Response |
1.0 µm |
1.6 µm |
5 µm |
3 to 5 µm |
3.9 µm |
3.43 µm |
Optical Resolution |
140:1 |
125:1 |
170:1 |
170:1 |
170:1 |
33:1 |
Emissivity |
0.1 to 1.00 digitally adjustable |
|||||
Focus Distance |
1.5m (60”) standard |
|||||
Optical Scan Rate |
20 to 150Hz |
|||||
Number of Samples |
512 data points per scan line (up to 80Hz ), 256 data points per scan line (80 to 150Hz) |
|||||
Outputs |
Analog: 3 user-configurable 0/4-20mA current outputs collectively isolated, Max. DC resistance 500Ω; Alarm: Electromechanical relay 30V, 1A; Digital Communications: RS485/RS232 full duplex, non-addressable; Ethernet Communication: TCP/IP protocol 10/100Mbit/s |
|||||
Inputs |
Trigger + 5 to 24VDC pulse (user-supplied) |
|||||
Power Supply |
24 VDC ± 25%, 1A |